The principle of full automatic filling machine, high precision liquid quantitative filling machine - is mechanical rotating, normal pressure filling, measuring cup quantitative, filling valve full closed, full automatic type of empty bottle transferred from the bottle line, through the cylinder wheel mechanism, the empty bottle is accurately delivered to the turntable, empty bottle immediately rotates. Through the soft support mechanism, the empty bottle is taken up and the bottle mouth is opened automatically after contact with the filling valve. The bottle is filled and the bottle is automatically pulled out into the bottle line. The whole process is finished. The machine is equipped with automatic protection device. If there is a phenomenon of bottle sticking, the machine will automatically stop and protect the safety of human-machine.
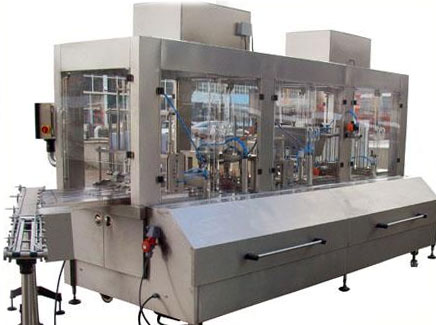
How to solve the faults of full automatic filling machine?
PLC fault
PLC failure is mainly due to the adhesion of output point relay contacts.
If the motor is controlled by this point, the motor runs after the signal is started by the motor, but the motor does not stop after the signal is stopped and the motor stops running when the PLC is out of power. If the point controls the solenoid valve, the failure phenomenon is that the coil of the solenoid valve is continuously energized, and the cylinder does not reset. If the external force hits PLC to separate the adhesion points, it can help to determine the fault.
There are two maintenance methods for the failure of PLC output point. A more convenient one is to use a programmer to modify the program. The damaged output point is changed to the standby output point and the line is adjusted at the same time.

Proximity switch fault
The filling machine has five close switches. The three is for knife protection, and the other two for controlling the upper and lower membrane release motors. Among them, one or two times of incorrect action are used to control knife protection. It will interrupt the normal operation process, and it will bring some difficulties to failure analysis and elimination due to the short number of failures and the short time. The cause of the failure is that the knives are not encountered during the descent. When the knife reaches the switch and loses the signal, it contacts the cutter head plate to the package, and the melting knife automatically returns upward. The fault repair method can install a switch of the same type in parallel with the switch and raise the position of the melting knife, so as to improve the reliability of the switch.
Malfunction of magnetic switch
The magnetic switch is used to detect the position of the cylinder and control the stroke of the cylinder. The four cylinder actions of stacking, pushing, pressing and melting knives are interrelated, and magnetic switches are used to detect and control their positions. The main trouble is that the following cylinder does not move, because the cylinder speed is relatively fast, resulting in the magnetic switch can not detect the signal. If the pushing cylinder speed is too fast, after pushing the bag to reset, the pressure pack and the cylinder do not move.
Malfunction of solenoid valve
The failure of solenoid valve is mainly due to the failure of the cylinder to operate or not reset, because the electromagnetic valve of the cylinder can not reverse or blow. If the solenoid valve is blowing, the air pressure of the machine can not reach the working pressure because the air inlet and outlet are connected. The maintenance method is to clean the solenoid valve and replace the damaged sealing ring.